Listen now
For decades, hardware development—combining software work and hands-on physical engineering—lagged behind its pure software counterpart. While software-only teams surged ahead with agile methods, cloud-based tools, and AI-driven automation, hardware engineers remained tethered to legacy systems, siloed workflows, and PDF or PPT-based collaboration. This gap in robust "software-for-hardware" tooling has driven many talented engineers toward software positions at Big Tech instead of pursuing mechanical or electrical-focused roles.
Now, 2025 marks the beginning of a hardware renaissance—thanks to AI unlocking a modern, integrated approach to developing physical products.
The rise of AI in hardware engineering
The rise of agentic capabilities and vertical-specific AI in hardware engineering are leveling the playing field—and in some cases, helping teams leapfrog even the fastest conventional design cycles. At the heart of this transformation is our thesis of “convergence,” where AI acts as a neural fabric across the hardware lifecycle, interlacing design, simulation, and manufacturing into a unified, self-optimizing organism. Companies that integrate intelligent tooling, embrace automation, and retrain their workforce for this symbiosis will see transformational benefits in speed, cost efficiency, and talent retention.
From the drawing board to the factory floor, AI is embedding itself into every step of the hardware product lifecycle—empowering engineers to tackle unprecedented complexity while enabling manufacturers to run flexible and resilient operations. For founders, investors, and industry leaders, this shift presents a generational opportunity to reimagine how products are designed, tested, and manufactured at scale—and a chance to pioneer the next frontier of hardware innovation!
The digital engineering value chain
Hardware development spans interconnected yet historically fragmented processes. Incumbents have dominated by acquiring tens to even hundreds of capabilities across the value chain (e.g., Autodesk has made over twenty acquisitions in the last decade):
1. Plan (Requirements Tracking & Management): Captures, prioritizes, and tracks product specs. These tools (e.g., Siemens Polarion, Jama Software) curate the blueprint and keep engineering efforts aligned from concept to completion.
2. Design & Engineer (CAD/CAE): Provides tools (e.g., Autodesk) for creating and refining mechanical and electrical designs with simulations and 3D modeling.
3. Simulate & Test (Simulation Tools, DAQ): Digital twin modeling and physics-based simulations (e.g., Ansys, Teradyne) to predict performance, validate design constraints, and reduce reliance on physical prototyping.
4. Source & Procure (ERP, Supply Chain Management): Manages procurement, vendor coordination, and material flow (e.g., SAP, Oracle) to ensure cost-effective, on-time production.
5. Collaboration (PLM, PDM, Project Management): Real-time communication and feedback (PTC, Siemens), version control, and process tracking—from concept through manufacturing—to ensure transparent progress monitoring, iteration, and accountability across disparate teams.
6. Build & Manufacture (MES, CAM): Automates and monitors the manufacturing process—integrating machines, workflows, and quality checks—for efficient product build and assembly.
7. Operate (CMMS, Predictive Maintenance, Work Instruction): Oversees asset performance, maintenance scheduling, and tribal knowledge capture. Real-time data and predictive analytics (e.g., Siemens, Emerson) mitigate downtime, control costs, and maintain safety across the production lifecycle.
Until recently, these workflows operated in silos with minimal collaboration or interoperability—and were highly manual with limited data-driven intelligence. CAD files might circulate via PowerPoint before being sent to PLM systems in different formats. Final manufacturing details are often coordinated over email—a lifecycle that remains error-prone and slow.
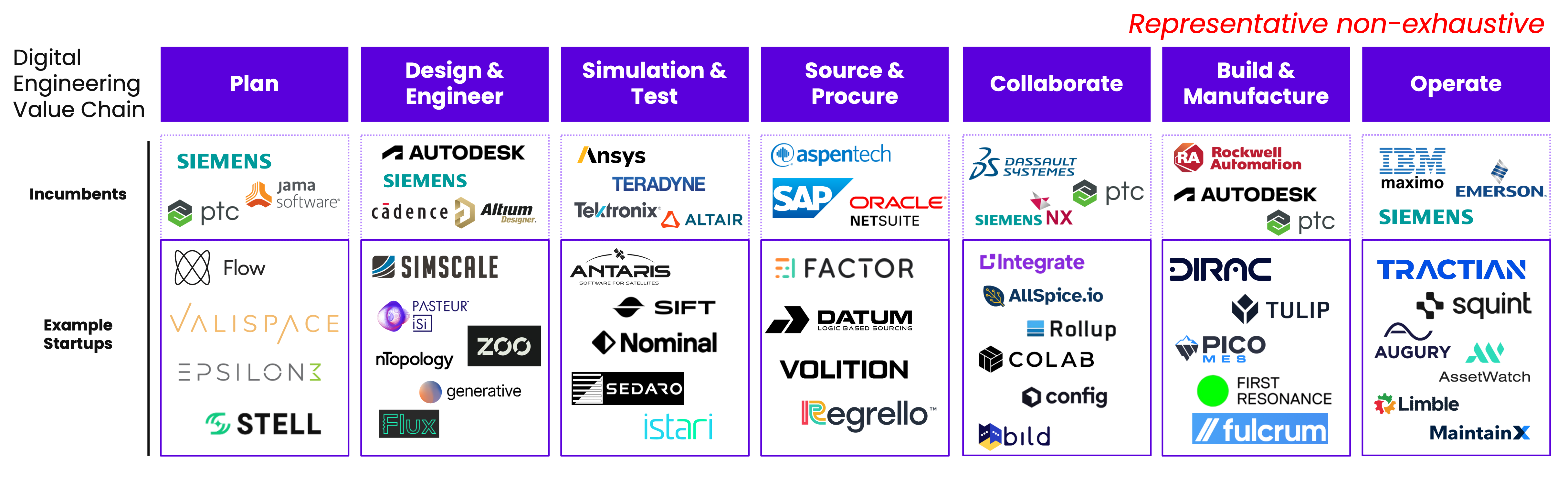
Why now? The convergence of talent, technology, and market drivers
AI adoption across hardware engineering is accelerating due to rapid tech advancements, market pressures, and cultural shifts. A 2024 Siemens study revealed that 92% of industrial leaders prioritize digital transformation. Engineering teams have captured ROI from early industrial automation but now face new forces driving change:
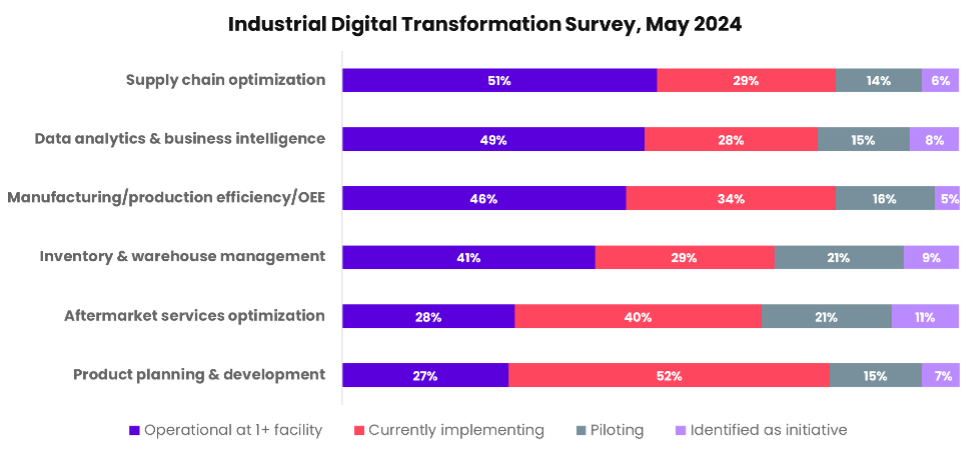
Tech Drivers
- Lower Cost of High-Performance Computing: Plummeting GPU prices coupled with step-function increases in performance make advanced AI simulations and generative design accessible to teams of all sizes.
- Cloud-Based Workflows: AI tools that once required costly on-prem hardware now run on flexible, scalable cloud platforms for real-time collaboration. Greater digitization and composable strategies are speeding up the adoption cycle of cloud-based solutions.
- Adaptable AI & Robotics: Models are more robust than ever, capable of handling complex engineering challenges like multiphysics simulation or real-time optimization across hardware development tasks. More performant generative design tooling and intelligent robotic systems have proved their ability to handle rising complexity and heterogeneity.
Market Drivers
- Geopolitical & Onshoring Pressures: As geopolitical fault lines fracture global supply chains, AI becomes the bridge between reshoring ambitions and the skilled labor gap—automating precision where human hands can’t scale. Cost pressures have become a forcing function to building higher levels of digitization and automation.
- Growing Product Complexity: Mass customization, sustainability imperatives, and advanced electronics push hardware designs to new levels of complexity. As more products become connected and intelligent, the reliance on the integration between hardware and software becomes even more paramount.
- Speed to Market: High competition requires compressed development cycles without sacrificing quality. Generative tooling can accelerate design, validation, and testing, enabling faster speed to market.
Talent & Workforce Drivers
- Software-First Engineering Culture: The next generation of engineers, weaned on generative tooling and shaped by experiences at Google, SpaceX, and other Big Tech incumbents, expect modern and agile practices that mirror software development.
- Open Collaboration: Emerging engineers require Git-like version control and real-time data sharing to eliminate the endless PDF email loops that once defined hardware workflows and limited execution speed.
- Automation and Digitization as a Workforce Multiplier: AI relieves skilled labor shortages and generational turnover by handling repetitive work and capturing tribal knowledge, allowing all functions to focus their expertise on driving innovation and optimization across higher-value tasks. Engineers want this!
How startups can build a sustainable business in the digital engineering ecosystem
- Target Critical Use Cases & Go Deep: Solve for critical use cases with a clear ROI. Whether it’s collaboration bottlenecks, BOM optimization, or testing/simulation challenges, winners will need to be ten times better than the status quo. As much as investors scream “platform,” focus on a specific area of the value chain will be key to dislodging scaled incumbents. The market runs with the herd, so once you’re in, the chances of moving horizontally to capture more value increases precipitously.
- Leverage Proprietary Data: Build integrations early and form necessary partnerships to access the data siloed across legacy systems, expert operators, and sometimes pen and paper. The startups that can effectively capture and digitize both tribal knowledge and critical data contained in siloed systems will have a sustainable advantage.
- User-Centric Design: Hardware engineers expect intuitive, flexible applications. The first wave of industrial automation and design solutions were hamstrung by long deployment times and over-engineered tooling. Ease of use and implementation coupled with quicker time-to-value through intuitive UI/UX is paramount to achieving broad adoption. The best strategy is to invest up front to make sure the first deployment is a resounding success (e.g. lighthouse strategy). That said, founders should be careful when deciding which customers or core systems demand ample engineering resources.
- Think Long-Term: Reengineering hardware design and manufacturing is not a quick fix; expect methodical adoption and disruption. With a shortlist of feature-rich incumbents dominating the ecosystem and operators historically hesitant to change, dislodging established players will take time. However, the payoff—especially for category-defining tools—can be significant.
Conclusion
AI is catapulting hardware engineering into an era of speed once reserved for software development. Generative design supercharges ideation; predictive analytics slashes downtime; inefficiencies are finally being eliminated. Yet this is just the beginning—the next few years will separate forward-thinking adopters from those clinging to legacy workflows.
At NGP Capital, we’re eager to partner with founders building toward this frontier. Hardware development is no longer an afterthought in this agentic revolution—it’s at its forefront. Startups that harness modern AI advancements will shape the next frontier of digital-physical innovation—and become the backbone of this hardware renaissance!
If you’re building toward this mission, let’s chat: eric@ngpcap.com! Stay tuned for part II as we explore how startups are already capitalizing on this revolution.